John Mannino is a skilled, self-taught Pennsylvania artisan who builds high quality acoustic guitars. “I always wanted to make guitars,” he told us. “I want to make as many as I can, of the highest quality I can.”
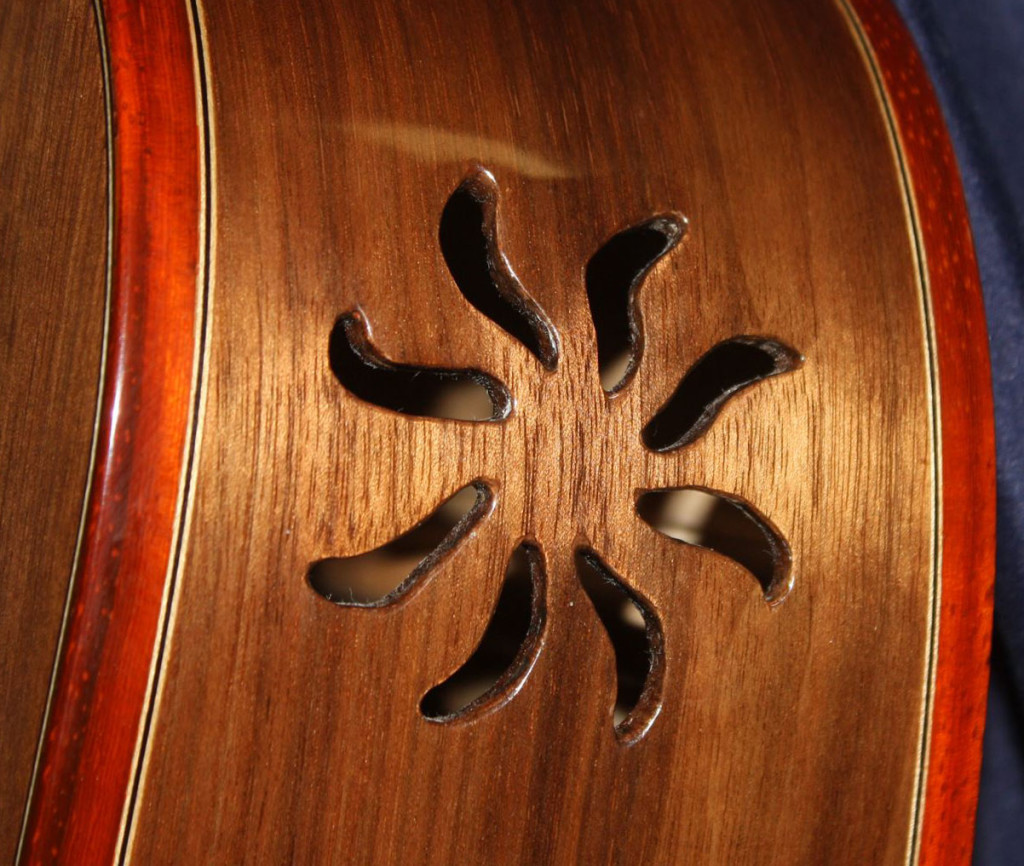
“Here’s a detail of a sound port on a dreadnaught-style guitar I made of local walnut with paduk trim.”
“I worked in construction for many years, hanging drywall and painting. I injured my back it gave me time to try what I’d always wanted to do, build acoustic guitars. Growing up, a friend’s father made violins. Maybe that inspired me.
Trial and error, and error, and error
I started making guitars about 14 years ago. I bought cheap equipment — a bandsaw, jointer, drill press, and so on at Lowe’s. I got a book on building guitars and started on this journey. I’m completely self-taught. I call it trial and error, and error, and error! It’s taken me a long time but my instruments are getting better and better. I’m getting good reactions from musicians.
Of course I play guitar myself — folk music, blues, jazz. A little bit of everything. But I don’t get that much time to play. I’m in the shop building guitars eight or ten hours a day. This is an avocation, something I want to do. And building quality guitars is a real challenge.
John makes them light and strong
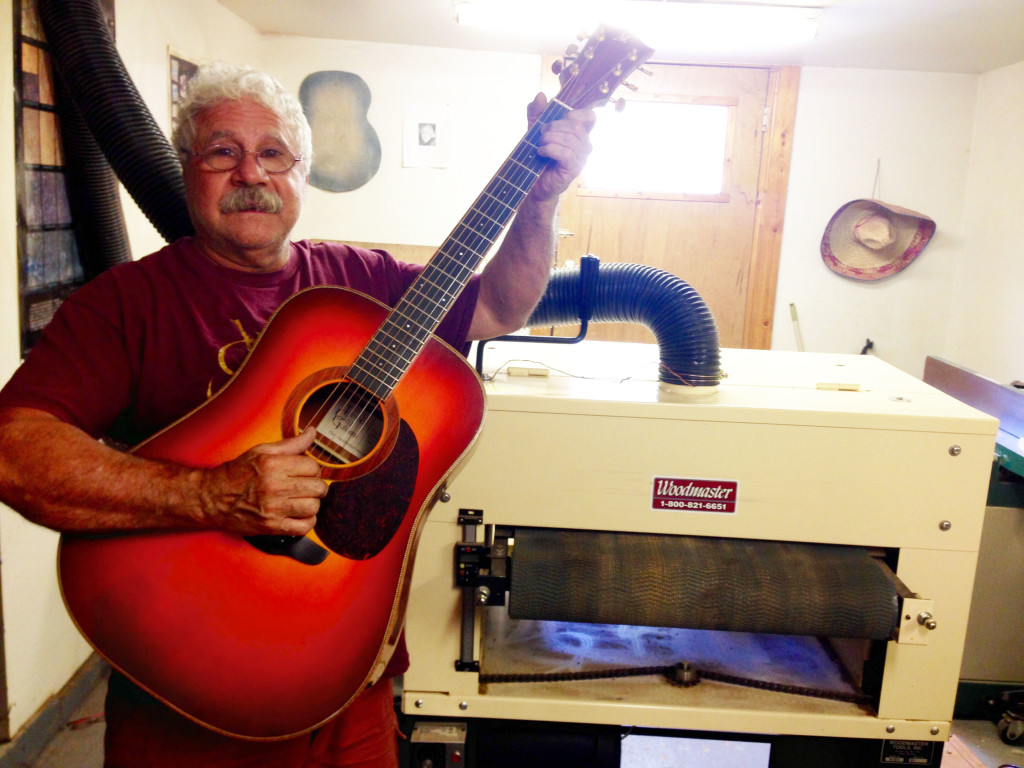
Here’s John with one of many guitars he’s made, and the Woodmaster Drum Sander he uses to make them.
Unlike an electric guitar, you have to build the sound into an acoustic guitar. You really have to know your wood. Different woods have different sounds, and you have to know how thin you can make the wood without having it collapse on you. You want a guitar to be light enough to be responsive but not so thin that they collapse.
SAVE BIG NOW on Woodmaster Drum Sanders! – sale prices, online specials
SAVE BIG NOW on Woodmaster Molder/Planers! – sale prices, online specials
I build every part of my guitars entirely by hand. Each guitar takes me a couple months to build. I made four this winter. I build the guitar itself then lacquer it, then let it set for two weeks to a month, then sand it down and buff it. Then I string it and let it set some more. Then I do the final setup, put strings on it, and play it. Of course while I’m waiting on one I can work on other ones.
When you’re into guitar making, there’s no such thing as too much wood. I buy wood all over. On the internet, at shows, at symposiums put on by ‘ASIA’ — the Association of Stringed Instrument Artisans. I work a lot with East Indian Rosewood, Honduran Mahogany, padauk, lacewood, ebony, and many more woods.
“This would be impossible without my Woodmaster Drum Sander.”
My Woodmaster Drum Sander is my most important piece of equipment. I couldn’t build guitars without it. It would be impossible to do what I do without my Woodmaster Drum Sander. When I started out, I got a Delta sander. It was $1,100 or so and was a big piece of junk. It kept breaking down, it was in the repair shop more than in my wood shop. My son did some research and learned about Woodmaster. The Woodmaster Drum Sander is built like a tank and is not that much more than Delta® and Grizzly® equipment that’s made in China.
I’m very satisfied and happy with my Woodmaster. It’s well used; I’ve had it four or five years and it’s never broken down. It’s very precise; I can sand wood down as thin as 80 thousandths of an inch. I make the backs of my guitars 100 thousandths. The sides are 80 to 90 thousandths.
For anybody doing delicate woodworking…
My goal in all this is to make as many guitars of the highest quality I can before they put me in the ground. Building a quality guitar is a real challenge! For anybody else who wants to make guitars, or anybody doing delicate work like this, I’d highly recommend getting a Woodmaster Drum Sander.”
— John Mannino, Woodmaster Drum Sander Owner, Lumber City Guitars, Reedsville PA
SAVE BIG NOW on Woodmaster Drum Sanders! – sale prices, online specials
SAVE BIG NOW on Woodmaster Molder/Planers! – sale prices, online specials
QUESTIONS? COMMENTS?
3 WAYS we can help you!
• Call us TOLL FREE 1-800-821-6651
• Email us info@woodmastertools.com
• Connect with us on Facebook
Links:
https://www.facebook.com/WoodMasterTools?fref=ts