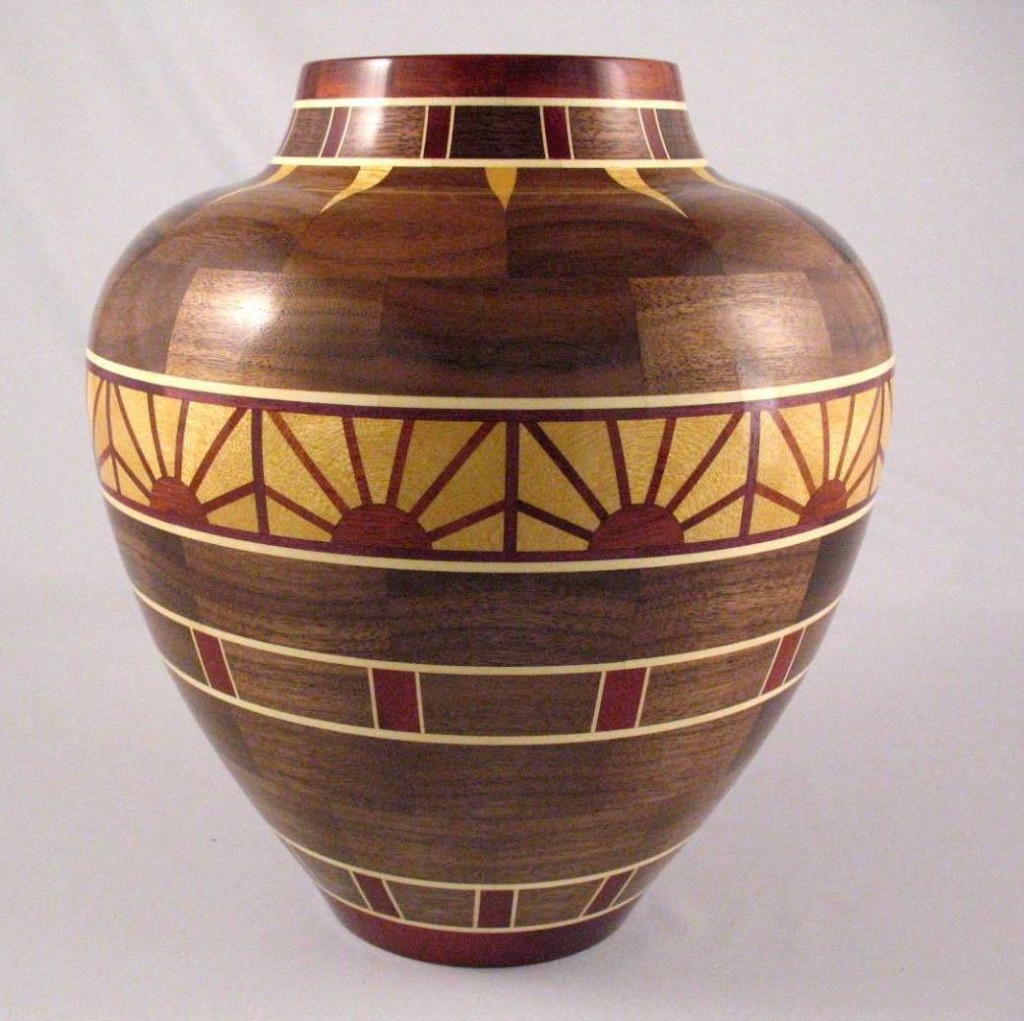
Pete Marken’s “Rising Sun” vase is 9-1/2” diameter X 10-1/2” tall – Woods used: Walnut, Yellowheart, Bloodwood and Holly. 551 pieces of wood
There’s “woodworking,” there’s “precision woodworking” and then there’s PRECISION woodworking. When you’re fitting together close to a thousand pieces of wood in a single project, and working with tolerances as tight as .005 inch, precision is everything. Woodworker, Pete Marken, sent us photos of his remarkable segmented woodturnings and we just had to know how he makes them…and how his Woodmaster Drum Sander helps his process. Here’s Pete’s story….
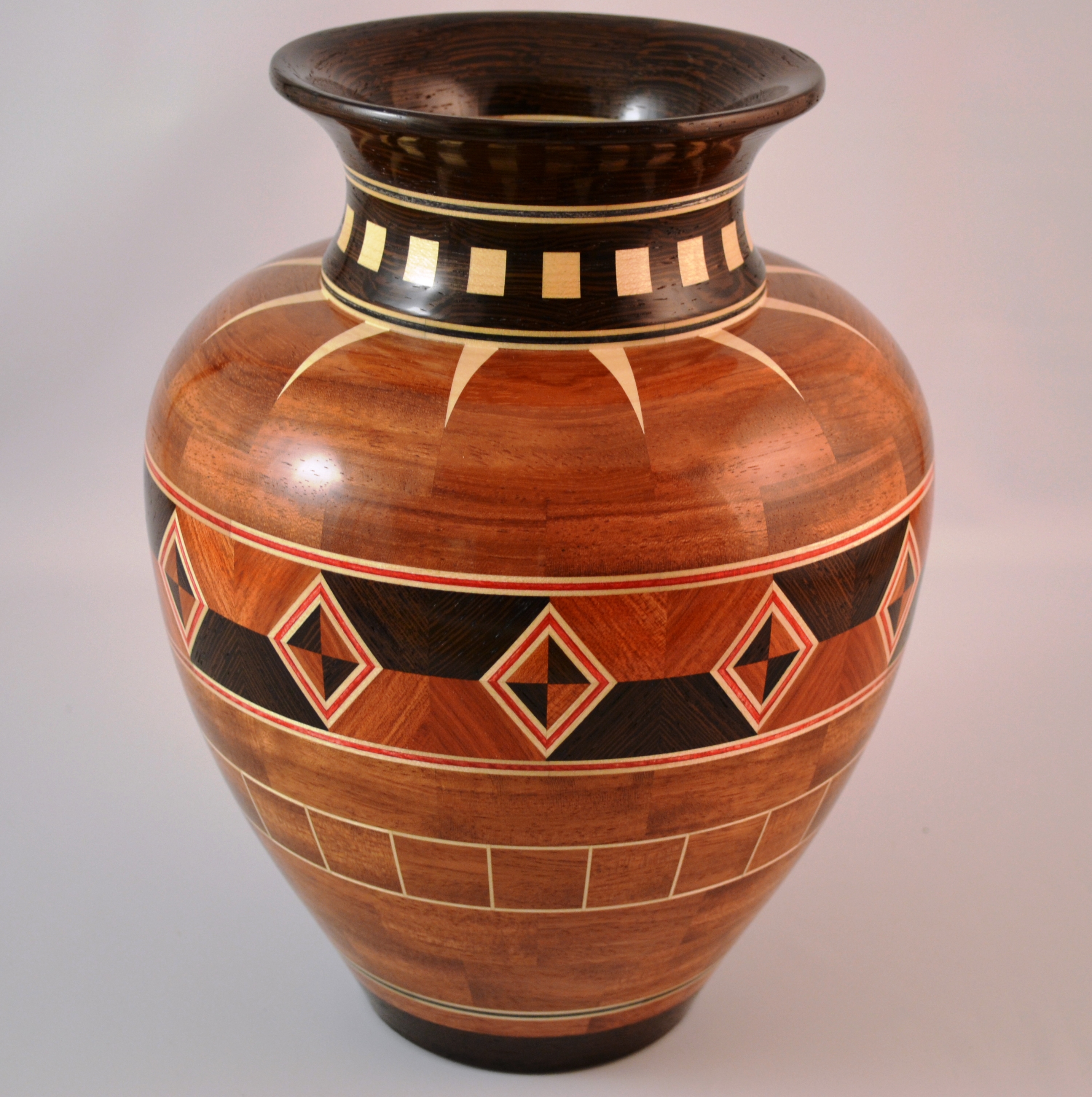
Vase with Diamonds – 8-1/4” diameter X 9-1/2” tall – woods used: Bubinga, Wenge, Maple and dyed veneers – 571 pieces of wood
“I started woodturning about 25 years ago and found I really enjoyed it more than any other kind of woodworking. I really got into it. Then, about five years ago, I started doing segmented woodturning.
Segmented woodturning is a really interesting style of woodturning where you assemble dozens or hundreds of wood segments in one project to create unique patterns. In conventional woodturning, you’re turning a solid piece of wood on a lathe. You’re working with one block of one type of wood. I found this was limiting what I could do compared to segmented woodturning.
SAVE BIG NOW on Woodmaster Drum Sanders! – sale prices, online specials
SAVE BIG NOW on Woodmaster Molder/Planers! – sale prices, online specials
870 little pieces of wood
I make my vases and bowls by cutting small segments of wood and gluing them to form rings. I stack and glue the rings, one on another. Then I turn the glued-up piece on my lathe. The challenging part is all the segments and all the rings have to be very precise so everything fits together exactly. If I’m off even two minutes of an arc, I’ll have a gap between segments or rings. (Editor’s note: 2 minutes of an arc equals 0.03 degrees!)
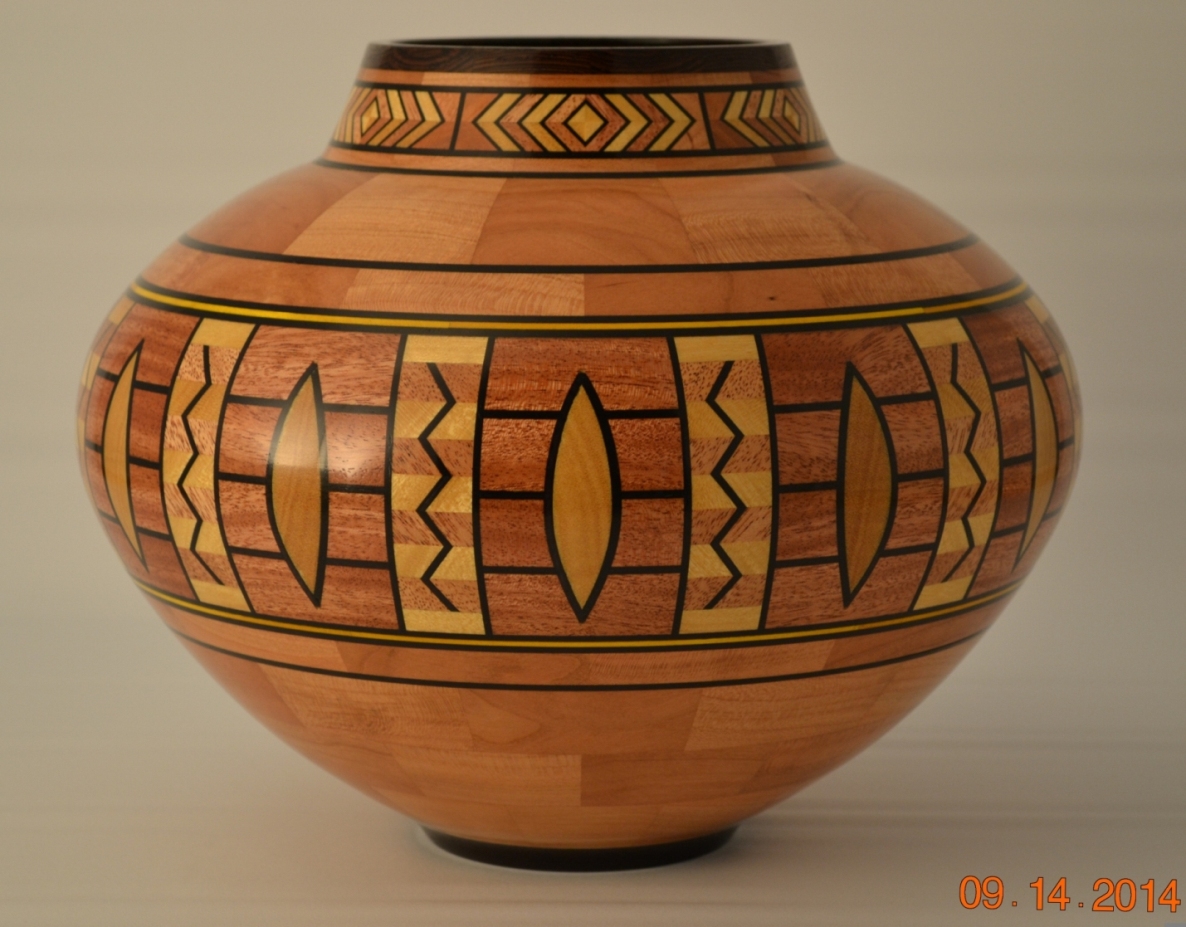
Vase – 11-1/4” diameter X 9” tall – woods used: Cherry, Mahogany, Yellowheart, Wenge and dyed veneer – 870 pieces of wood
The rings with all the design work in them are called ‘feature rings.’ The designs in them have to be cut very precisely, too. One segment may have 20 to 30 or more pieces of wood in it. One of my vases is made of over 870 individual pieces of wood!
I’ve sold my turnings through word of mouth, galleries, and I do custom work, too. Prices for some of my turnings can range up to $1,200 or more depending on complexity of the design and the wood I use. For example, Ebony is very expensive – up to $120 or $140 a board foot.
Woodmaster’s “closed-end” design keeps drum and conveyor belt completely parallel
I bought my Woodmaster 2675 Drum Sander specifically for this work. I use it to clean up boards after I resaw them on my bandsaw. And I use it to make my rings flat and of uniform thickness. Precision is key — I work within five thousandths of an inch, 0.005. (Editor’s note: 0.005 inch, as a fraction, is 1/200 of an inch!)
I did my research and found Woodmaster is more robust, solid, and stable than other sanders. It’s sturdy, good and heavy, and paper changes are easy, too.
“My 26” Woodmaster is a good size for my work and my shop.”
I had other drum sanders but I chose Woodmaster because it’s a ‘closed end’ design, not like cantilevered sanders where one end of the drum is open and not secured. With cantilevered drum sanders, you have issues with the sanding drum not being parallel to the conveyor belt. Then your workpiece ends up being thinner on one side than the other. My Woodmaster’s drum is always level and parallel to the conveyor belt.
Because the drum is held at each end, you can have a wide drum. This 26” machine is a really good size for me, and the machine’s a good size for my shop. I’m happy and I’d tell woodworkers who’re thinking about getting a drum sander to definitely take a look at Woodmaster.”
— Pete Marken, Woodmaster Drum Sander owner, is a member of the Alabama Woodturners Association; the American Association of Woodturners; and the Segmented Woodturners Association.
Visit Pete’s website and his Facebook page.
SAVE BIG NOW on Woodmaster Drum Sanders! – sale prices, online specials
SAVE BIG NOW on Woodmaster Molder/Planers! – sale prices, online specials
QUESTIONS? COMMENTS?
3 WAYS we can help you!
- Call us TOLL FREE 1-800-821-6651
• Email us info@woodmastertools.com
• Connect with us on Facebook